As someone with extensive experience in the field of logistics and supply chain management, I understand the significance of accurately tracking orders and maintaining efficient delivery schedules. An important aspect of this process is understanding the ship date and its impact on the entire supply chain. To ensure a smooth shipping experience, it is crucial to grasp the concept of ship date and how it affects the overall delivery timeline.
So, what exactly does ship date mean? Ship date refers to the date when a shipment leaves the warehouse or point of origin, and it marks the beginning of the delivery process. This date is essential because it helps determine the estimated delivery time, allowing customers to plan accordingly. Moreover, it enables businesses to optimize their supply chain operations and minimize the risk of delays or other issues. By following this article, you will gain valuable insights into the importance of ship date and learn how to manage it effectively for a seamless shipping experience. So, let’s dive in and explore the world of ship dates!
What is a Ship Date and Why Is It Important?
A ship date is the scheduled date when a shipment leaves the warehouse or point of origin, marking the start of the delivery process. This critical aspect of shipping plays a vital role in determining the estimated delivery time for customers and optimizing supply chain operations for businesses. By understanding and managing ship dates effectively, both customers and businesses can minimize the risk of delays, maintain efficient delivery schedules, and enhance overall satisfaction.
Ship dates have a direct impact on the overall performance of a supply chain. They are crucial for setting accurate delivery expectations, which help customers plan for the arrival of their packages. An optimized ship date schedule also enables businesses to allocate resources more efficiently, such as warehouse storage space, labor, and transportation. This, in turn, leads to cost savings and improved customer service.
Recent studies show that 69% of consumers are less likely to shop with a retailer in the future if an item is not delivered within two days of the expected delivery date. This highlights the importance of accurately estimating and communicating ship dates to customers. By effectively managing ship dates, businesses can build trust and loyalty among their customer base, ensuring repeat purchases and long-term success.
Factors Affecting Your Order’s Ship Date
Several factors can influence the ship date of your order, impacting the overall delivery timeline. These factors can be internal or external and may vary depending on the nature of the product, the shipping method chosen, and the distance between the point of origin and the destination.
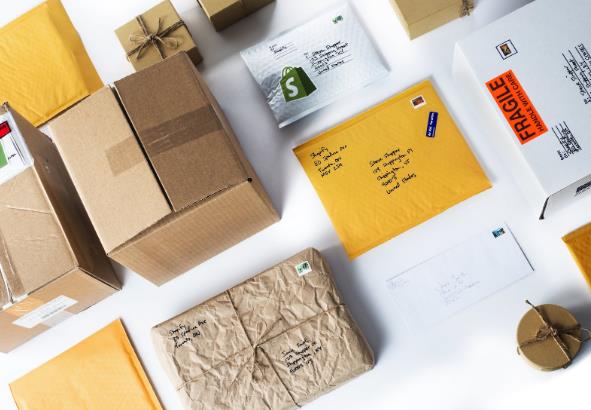
What Does Ship Date Mean and Its Impact on Deliveries
Some common factors affecting ship dates include:
- Inventory availability: If a product is out of stock or has limited availability, it may take longer for the warehouse to prepare the shipment.
- Order processing time: The time it takes for a business to process and prepare an order for shipment can also impact the ship date. This can include tasks such as picking, packing, and labeling the products.
- Shipping method: Different shipping methods have varying transit times, which can affect the overall delivery timeline. For example, expedited shipping options may have shorter transit times compared to standard shipping methods.
- Customs and regulations: For international shipments, customs clearance and compliance with local regulations can cause delays in the shipping process, consequently affecting the ship date.
- Weather and natural disasters: Extreme weather conditions or unforeseen natural disasters can disrupt transportation networks, leading to delays in shipping and changes in ship dates.
- Carrier capacity: During peak seasons or due to other circumstances, carriers may experience capacity constraints that can lead to delays in picking up shipments, impacting the ship date.
By understanding these factors, customers and businesses can better anticipate potential delays and manage their expectations accordingly. Moreover, businesses can implement strategies to mitigate the impact of these factors on their supply chain operations and maintain efficient shipping schedules.
How to Calculate the Ship Date for Your Order
Calculating the ship date for your order is essential for setting accurate delivery expectations and making necessary arrangements to receive your package. The ship date is determined by several factors, including inventory availability, order processing time, shipping method, and carrier capacity. By understanding these factors, you can estimate the ship date for your order and plan accordingly.
To calculate the ship date for your order, follow these steps:
- Check inventory availability: Ensure that the product you ordered is in stock or available for shipment. If it is out of stock or has limited availability, expect a delay in the ship date.
- Consider order processing time: Take into account the time it takes for the business to process and prepare your order for shipment. This includes tasks such as picking, packing, and labeling the products.
- Select the shipping method: Choose a shipping method that best suits your needs and consider the transit time associated with each option. Expedited shipping options usually have shorter transit times compared to standard shipping methods.
- Factor in customs and regulations (if applicable): For international shipments, consider the time it may take for customs clearance and compliance with local regulations, which can cause delays in the shipping process.
- Monitor weather conditions and carrier capacity: Keep an eye on extreme weather conditions or unforeseen natural disasters that may disrupt transportation networks. Also, be aware of potential carrier capacity constraints during peak seasons or other circumstances, which can lead to delays in picking up shipments.
By taking these factors into account, you can better estimate the ship date for your order and manage your expectations accordingly. This will help ensure a smooth and stress-free shipping experience for both customers and businesses.
The Role of Ship Date in Supply Chain Management
The ship date plays a crucial role in supply chain management, as it directly impacts the efficiency of order fulfillment processes and customer satisfaction. Accurate ship dates enable businesses to optimize their resources, such as warehouse storage space, labor, and transportation, leading to cost savings and improved customer service. Furthermore, managing ship dates effectively helps businesses build trust and loyalty among their customer base, ensuring repeat purchases and long-term success.
Effective ship date management allows businesses to:
- Set accurate delivery expectations: By providing customers with precise ship dates, they can plan for the arrival of their packages and minimize the risk of missed deliveries or dissatisfaction.
- Optimize inventory management: Accurate ship dates help businesses maintain an optimal balance between inventory levels and customer demand, reducing the risk of stockouts or overstocking.
- Improve carrier relationships: Timely and accurate communication of ship dates with carriers enables better coordination and collaboration, resulting in more efficient transportation networks and reduced costs.
Overall, the ship date is a vital component of supply chain management, and businesses must prioritize its accuracy and optimization to ensure smooth shipping operations and maintain customer satisfaction.
Common Reasons for Ship Date Delays and How to Avoid Them
Ship date delays can occur due to various reasons, impacting the overall delivery timeline and customer satisfaction. By understanding the common causes of these delays, businesses can implement strategies to prevent or mitigate their impact on the supply chain, ensuring a smooth shipping experience for their customers.
Some of the most common reasons for ship date delays include:
- Inventory shortages: Running out of stock or having limited availability of a product can cause delays in preparing shipments. To avoid this issue, businesses should maintain accurate inventory records and implement effective demand forecasting techniques.
- Inefficient order processing: Slow or disorganized order processing can lead to delays in picking, packing, and labeling shipments. Businesses should invest in warehouse management systems and staff training to improve efficiency.
- Carrier capacity constraints: During peak seasons or due to other circumstances, carriers may experience capacity constraints that can delay shipment pickups. To prevent this, businesses should work closely with their carriers to plan for peak periods and explore alternative shipping options if necessary.
- Customs and regulatory issues: International shipments may face delays due to customs clearance or compliance with local regulations. Ensuring proper documentation and understanding the specific requirements for each destination can help minimize these delays.
- Extreme weather conditions or natural disasters: Unforeseen events like extreme weather or natural disasters can disrupt transportation networks. Businesses should have contingency plans in place to reroute shipments or find alternative carriers when necessary.
By proactively addressing these potential causes of ship date delays, businesses can maintain efficient shipping operations and ensure customer satisfaction. Implementing strategies to prevent or mitigate these issues will not only enhance the overall supply chain performance but also contribute to long-term business success.
To Wrap Up
In conclusion, understanding and managing ship dates effectively is crucial for maintaining efficient delivery schedules and ensuring customer satisfaction. By considering factors such as inventory availability, order processing time, shipping method, customs, and carrier capacity, businesses can optimize their supply chain operations and minimize the risk of delays. Implementing strategies to prevent or mitigate ship date delays will not only enhance the overall supply chain performance but also contribute to a positive customer experience.
As customers and businesses become more knowledgeable about the importance of ship dates and how they impact the delivery process, smoother and more efficient shipping experiences can be achieved. With accurate ship date estimations and proactive management, both customers and businesses can look forward to timely deliveries and an overall positive impact on their satisfaction and success.
Frequently Asked Questions
[faq-schema id=”1005″]